Shayleigh Faye
TTM 517: Advanced Computer-Aided-Design for Fashion
This graduate-level course focused on the full digital development of sustainable apparel—from concept sketches to 3D garment simulation. Through a combination of Adobe Illustrator, Gerber AccuMark, and Clo3D, I built technical flats, engineered patterns, created virtual prototypes, and developed a full sustainable collection.
For my final project, I created Fika: a knitwear line inspired by the Swedish ritual of slowing down. Featuring modular silhouettes and cozy structures, Fika utilized recycled polyester, waterless digital dyeing (Twine), and an entirely digital product development pipeline to minimize material waste. The project was submitted to the AATCC C2C Design Competition, emphasizing market-driven design, technical precision, and environmental responsibility.
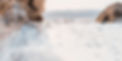
Technical Flats – Adobe Illustrator
Using Adobe Illustrator, I developed detailed technical flats for three key garments in my Fika collection: a modular turtleneck shirt, an oversized tunic, and a lightweight skirt. Each flat drawing captured essential construction details such as seam placement, ribbing, pointelle textures, and modular sleeve attachments.
Through the use of Illustrator’s pen tool, pathfinder functions, and live paint features, I ensured that each design clearly communicated fit, silhouette, and garment engineering—providing an essential foundation for pattern development and 3D simulation later in the process.
PGM Programming – Shima Seiki SDS-ONE APEX
After completing my technical flats, I transitioned into Shima Seiki’s PGM software to program the knitted structures for each garment. Using SDS-ONE APEX, I created detailed knitting programs for the turtleneck, tunic, and skirt—optimizing structures for both visual texture and functional performance.
Through precise stitch mapping, inlay techniques, and digital yarn simulations, I developed panel-knit designs that reduced material waste and enhanced garment adaptability. This process allowed me to virtually test and refine construction details before physical production, reinforcing the collection’s sustainable and modular design philosophy.

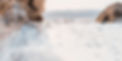
Virtual Prototyping – CLO3D
To finalize garment development, I imported my patterns into CLO3D to create virtual prototypes of the turtleneck, tunic, and skirt. In CLO, I adjusted fit, simulated fabric properties, and visualized layering possibilities—all without physical sampling.
By applying custom fabric textures, trims, and colorways, I was able to refine the look, movement, and construction of each piece. This digital prototyping process ensured design accuracy, enhanced sustainability by minimizing material waste, and brought the Fika collection to life in a fully virtual environment.